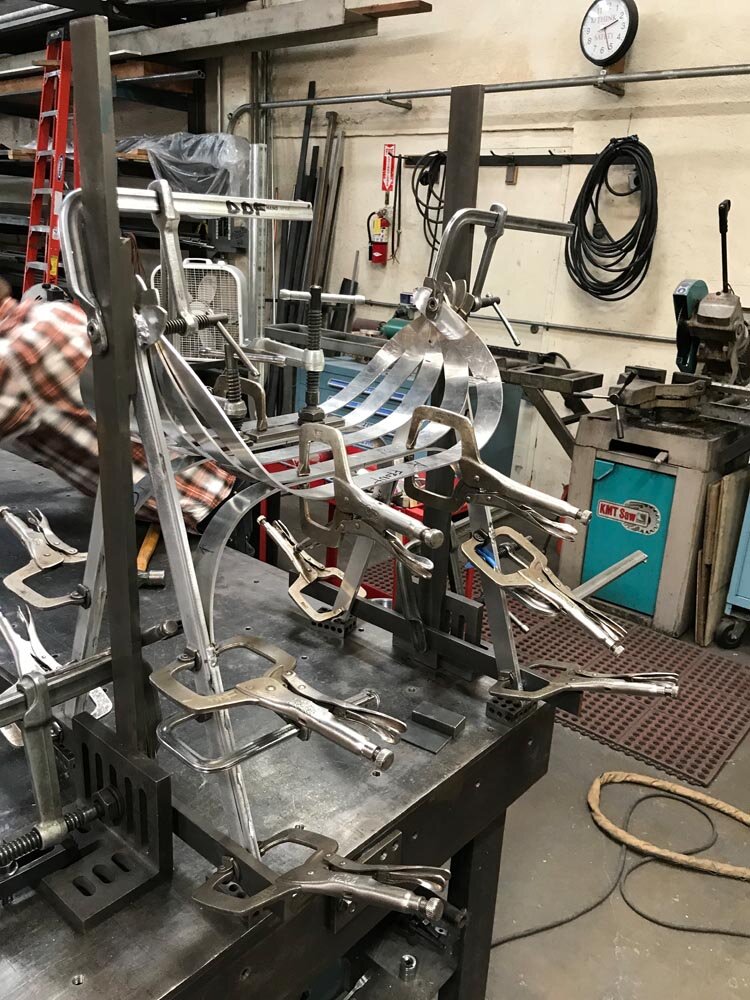
Chair Process
The process for each of these chairs was wildly divergent from each other. The hand bent and seamlessly welded aluminum chair began in CAD, then water jet the parts, then the meticulous and arduous process of perfectly making all pieces come together and weld in place.
The Process for the bent wood laminate chair of the same design began like a dress maker cutting out a pattern in wood veneers. Then the glueing and pressure molding around the “void molds”. The hardest part was figuring out how to join the separate ribs so that there was srength and structural integrity to the chair.
Both pieces have there merits, I personally prefer the aluminum one as it is a more successful example of the original design intent.
Side by side.
Hand bending the laminates to a set arch with Carly
Model making; discovery and inspiration
Turning a 3-D form into a 2-D template the old fashioned way.
The compound curved ribs of the chair needed a more complex method for lamination. I had to make the negative space shape for the rib to be formed around. Then everything went into a pressure bag for 24 hours to make sure it sets correctly.
Back from the water jet; components ready to hand bend.
Letting my laminates cure and set for a day or two...
Always begins here....